
Furniture quality interior doors
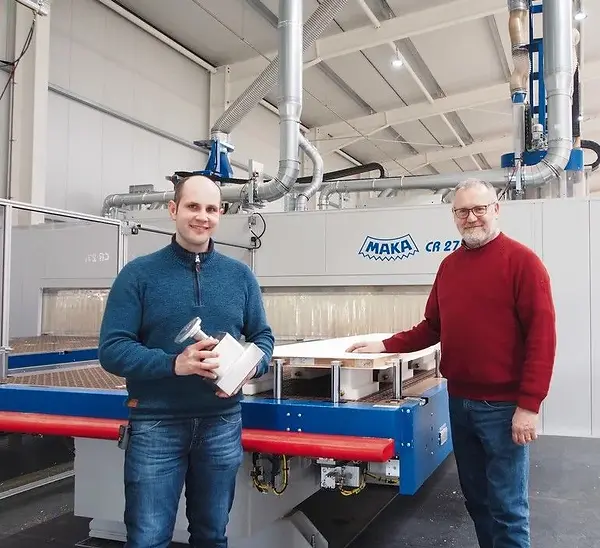
Nießing produces interior doors in furniture quality using state-of-the-art technology
Highly flexible
Nießing, a door manufacturer based in Borken, has put part of its production on a new, extremely strong footing. The new panel storage facility automatically feeds both the horizontal saw and the new high-performance CNC. This may sound like "mass production" at first, but it has a completely different background: the state-of-the-art technology enables the flexible and precise production of completely individual interior doors that are of the highest quality right down to the last detail.
Nießing produces high-quality interior doors on a total of around 10,000 m2 in Borken in the northwest of North Rhine-Westphalia near the Dutch border. The family business is run by Josef Nießing (66) and his son Jonas (33). Last year, the two master carpenters invested heavily in a new production hall and state-of-the-art machine technology, thereby setting the course for the future.
Strong partner for trade and industry
​
The company specialized exclusively in the production of interior doors as early as the 1970s. Initially, these were special elements for the door industry on a large scale. From 2000 onwards, Nießing then invested specifically in the development of its own brand. This enabled the company to establish itself as a supplier of high-quality interior doors, particularly among carpenters and joiners. This area now makes a significant contribution to sales, and the trend is rising. Josef Nießing: "Our high quality level and great flexibility are particularly popular with our carpenters and joiners. So you won't find a 250 euro door here."
More than 200 carpenters and joiners now rely on a partnership with Nießing. The company continues to be a highly sought-after and reliable supplier and partner for special solutions, even as a supplier to industry.
​
Josef Nießing's wife Mechthild, who takes care of marketing, sums up what the family business stands for: "We see ourselves as partners of our customers from the carpentry trade and the door industry. The goal must always be to achieve long-term success together."
​
The company employs 44 people. Training is also very important in the carpentry guild. Josef Nießing: "We always have four to five trainees. It is important to us that they work for us on a trial basis or do an internship beforehand."
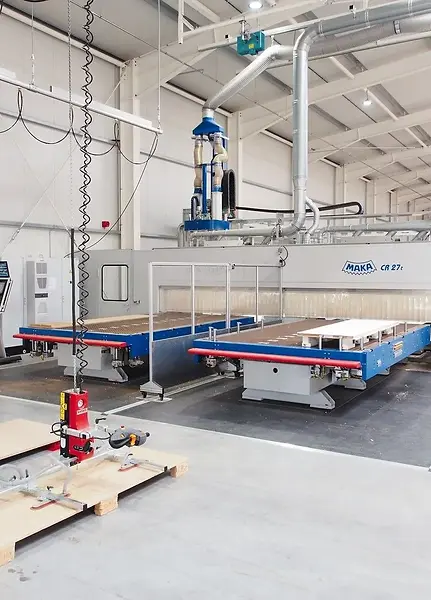
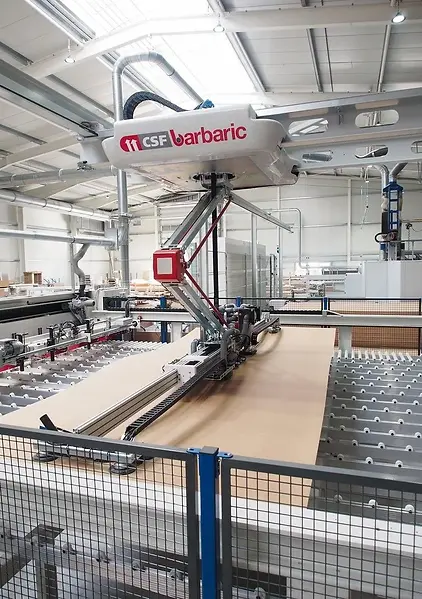
Automatic warehouse feeds saw and CNC
​
Last year, Nießing expanded its production by a 2500 m2 hall. Reason: Panel cutting and CNC processing have been taken to a new level. The centerpiece is a fully automatic panel storage system CSF from Barbaric. This feeds both the Schelling fh 4 panel dividing saw and the high-performance CR 27t CNC machining center from Maka.
Jonas Nießing is very satisfied: "With the Barbaric storage we can handle practically all panels up to 300 kg that we process - even very difficult ones. To make this work, Barbaric wrote more than 25 programs for the manipulator. In the near future, this will be made fit for handling wood fiber insulation boards with needle grippers.
​
Nießing currently occupies around 60 spaces in the 35 m long warehouse, sorted as well as chaotically or by order. These are full, half and any other formats, but also semi-finished parts and leftovers. Thanks to the 90° turning unit, the panels can be stored in all directions. The panels are measured and weighed during each restacking process. Also on board the Barbaric camp is the Labeling Printer LPS. With this unit, panels can be labeled before they are cut.
Individually configured high-performance CNC
​
A real highlight in the new hall is the new Maka CNC machining center. Together with Michael Meer, Maka Sales Manager North, Josef and Jonas Nießing spent hours and half nights thinking, sweating and discussing. In the end, they have defined a very individually configured machine that meets the high standards of quality and performance.
​
The 5-axis CNC machining center CR27 t has two moving tables in tandem design that can be coupled if required. The working area (cube dimensions) with a total tool length of 200 mm and a tool diameter of 60 mm is 2200 x 4100 x 400 mm per table. The center aisle between the two tables allows loading from three sides: manually from the front or from the side of the table, and fully automatically from the back of the panel storage. This offers the door manufacturer extremely high flexibility. The machine tables have an extended extension stroke. This means that the Maka can be loaded automatically from the panel storage without any problems.
​
Father and son are real technology freaks and explain the many exciting details of the machine to me. They were particularly taken with one thing: the 5-axis spindle (26 kW) with the galaxy drive system from Wittenstein. "The spindle is awesome because it is completely free of play and enables us to achieve a very high machining performance."
The phenolic resin grid tables are equipped with milled grooves for inserting sealing cords. Each table has seven longitudinal workpiece stops that can be lowered pneumatically, designed as lifting and swiveling cylinders with a stop tongue for overhanging veneers. The machine has a large number of special equipment details, including:
​
-
14 vacuum clamping circuits per machine table
-
Additional 4-axis milling spindle HSK F63, 26 kW
-
Chain tool magazine with 33 places for 5-axis unit
-
two turntable tool magazines with 20 places each for the 4-axis unit
-
one suction bar with automatic lift per table (0 – 400 mm, variably adjustable)
-
two automatic tool measurement and breakage detection systems with laser beam
-
3D probe with radio transmission
-
Camera system for process monitoring
-
Maka contour laser projection system.
-
Machine-independent CAD/CAM software
​
For the design and machine connection, the door manufacturers use a combination of AutoCAD and the machine-independent CAM software NC-Hops for door production from Direkt CNC-Systeme. Jonas Nießing: "Now that we are well positioned in terms of machine technology, we are currently working intensively on new CAD software."

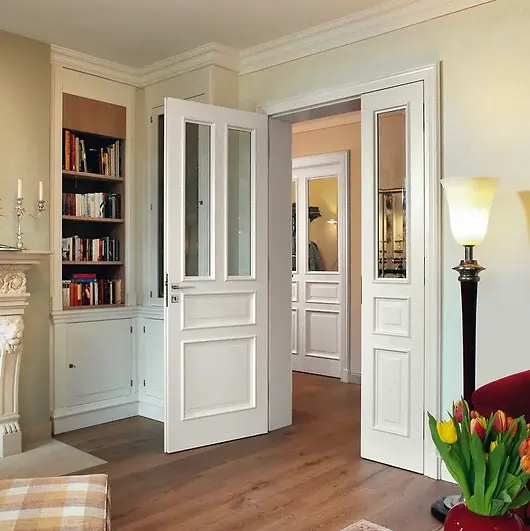
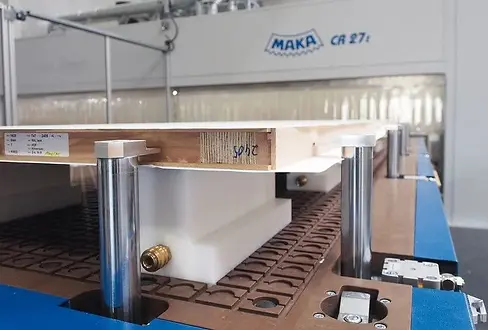

KeraTür investiert in 5-Achs-CNC-Komplettbearbeitung für Türblätter
Handwerk trifft Technik​
​
Mit einer außergewöhnlich hohen Wertschöpfungstiefe produziert KeraTür in Raesfeld hochwertige Haustüren in allen Stilrichtungen und mit interessanten Alleinstellungsmerkmalen. Für die flexible Komplettbearbeitung der Türblätter hat das Unternehmen in eine 5-Achs-CNC von Maka investiert – was u. a. einen deutlichen Produktivitätsschub mit sich brachte.
​
KeraTür macht nur eines, aber das besonders gut: Haustüren aus Holz. Diese bieten u. a. passivhaustaugliche Wärmedämmwerte ab 0,64 W/m2K sowie Sicherheitsklassen bis RC3. Wichtigste Säule ist die enge Zusammenarbeit mit der Fertighausindustrie. Ebenso werden Privatkunden bedient – inklusive Beratung in der Ausstellung sowie Montage und Service vor Ort. Auch für Händler und Tischler empfiehlt sich das Unternehmen als Partner. Julian Kemming (40), dessen Urgroßvater die Tischlerei gründete: „Bei uns trifft flexible Maschinentechnik auf traditionelle Handarbeit.“
​
In Sachen Konstruktion wird auf Entwicklungen aus dem eigenen Haus gesetzt. Als Türrahmen kommt ein eigens entwickeltes Blockzargensystem mit 120 mm Profilstärke anstatt eines herkömmlichen Blendrahmens zum Einsatz. Das ist ein interessantes Alleinstellungsmerkmal in puncto Stabilität und auch Optik, da alle Rahmenriegel die gleiche Ansichtsbreite im eingebauten Zustand haben. Die Türblätter sind 94 mm dick und in zweischaliger Verbundbauweise ausgeführt.
Die Produktpalette reicht vom preisbewussten Serienprogramm bis hin zu individuellen High-End-Lösungen. KeraTür wurde bereits viermal mit dem RedDot-Design-Award für innovatives Produktdesign ausgezeichnet. Attraktiv in Szene gesetzt wird das Portfolio in der hauseigenen, 200 m2 großen Ausstellung am Firmensitz in Raesfeld.
​
​​Sehr hohe Wertschöpfungstiefe
Mit seinen insgesamt rund 70 Mitarbeiterinnen und Mitarbeitern – davon 50 in der Produktion – setzt der Haustürhersteller auf eine extrem hohe Fertigungstiefe. Gekauft wird das Schnittholz direkt beim Sägewerk. Nach sechsmonatiger Freiluftlagerung wird das Holz in modernen Kammern schonend getrocknet und dann erst im eigenen Betrieb entsprechend weiterverarbeitet. Ob Kanteln, Türrohlinge, Füllungen, Aufdoppelungen und mehr: KeraTür produziert all diese Komponenten komplett selber, um keinerlei Kompromisse in Sachen Qualität bei den jährlich insgesamt rund 3500 bis 4000 produzierten Haustüren eingehen zu müssen. „Das hat auch mit Termintreue zu tun, die wir sehr großschreiben“, so Julian Kemming. „Wir liefern zuverlässig innerhalb von drei Wochen ab Bestellung. Das schaffen wir nur, weil die komplette Lieferkette im eigenen Haus ist.“ Um das zu realisieren, ist auch ein sehr flexibler und leistungsstarker Maschinenpark erforderlich.
​
Flexible Komplettbearbeitung der Türblätter
Die CNC-Bearbeitung der Kanteln wird seit 2014 auf einer Conturex aus dem Hause Weinig ausgeführt. Die Türblattbearbeitung erfolgt seit 30 Jahren zuverlässig auf einem CNC-Bearbeitungszentrum mit zwei Tischen der Fa. Heian. Um flexibler auf die stetig gewachsene Auftragslage mit höheren Produktionskapazitäten zu reagieren, hat man sich zur Investition in ein zweites CNC-BAZ entschieden. Zunächst wurden dazu alle namhaften CNC-Hersteller am Markt gescreent. Aufgrund der hohen Zerspanungsleistung beim Fräsen von bis zu 150 mm dicken Türblättern braucht es eine sehr robuste Bauweise. Daher kam nur eine schwere Tischmaschine mit festem Portal infrage. Kemming: „Nach dem ersten Gespräch mit Michael Meer von Maka Nord war klar, dass Maka der richtige Partner für uns ist.“ Das Unternehmen entschied sich für das 5-Achs-Bearbeitungszentrum CR 27s. „Gemeinsam mit Michael Meer haben wir eine optimale Lösung für uns erarbeitet.“
Zudem hat Kemming sich intensiv mit Kollegen, beispielsweise mit dem Innentürhersteller Nießing aus dem nahegelegenen Borken, ausgetauscht, der ebenfalls auf Maka-CNC-Technologie bei der Türblattbearbeitung setzt.
​​

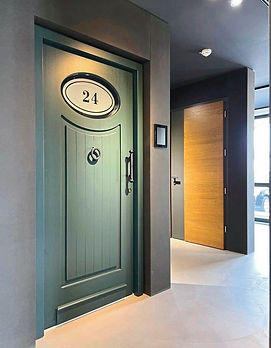
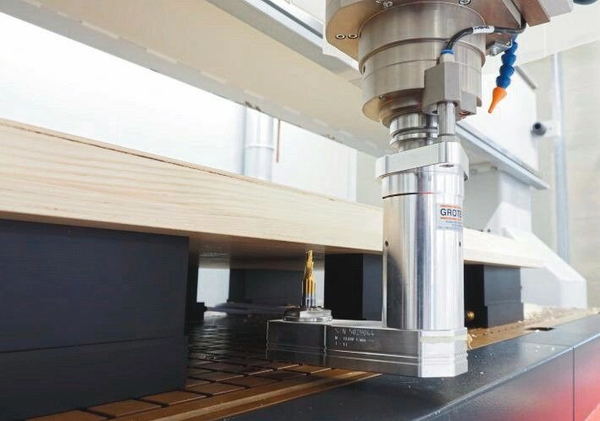

​​​Starke Features, unkomplizierte Anbindung
Die Maka bietet einen flexiblen Arbeitsbereich von 3000 x 1500 x 400 mm. An Bord hat sie ein Hightech-5-Achs-Universalaggregat mit Galaxie-Antrieb und einer Leistung von 26 kW. Die sehr hohe Verdrehsteifigkeit und Nullspiel sorgen für hochpräzise Bearbeitungsergebnisse.
Für das Spannen auf dem Rastertisch wurden spezielle Vakuum-Blocksauger entwickelt. Als Anschlag kommen absenkbare Anschlagbolzen zum Einsatz. Diese lassen sich noch um 90° verdrehen, falls das Werkstück einen Falz- bzw. Furnierüberstand hat. Zudem hat sich die Laser-Positionierung von Sauger und Werkstück bewährt. Der Kettenwerkzeugwechsler hat 51 Plätze. Hinzu kommt ein zusätzlicher Pick-up-Platz für drei weitere große Werkzeuge bzw. Aggregate. Die Bohr- und Fräsaggregate lieferte – wie zuvor bereits für die Heian und Conturex – die Fa. Grotefeld. „Auch hier lief die Abstimmung hervorragend und mit der Performance sind wir sehr zufrieden.“ Um das manuelle Schleifen auf die Maschine zu verlagern, hat man sich an den Schleifexperten Arminius gewandt. „Die für uns entwickelten Schleifaggregate arbeiten sehr präzise und mit einer langen Standzeit. So wird dieser sonst zeitaufwendige Arbeitsschritt den Kollegen im Bankraum erspart.“
​
Angesteuert wird die Maka (sowie auch die Conturex) von der CAD/CAM-Software Alphacam. Julian Kemming: „Das ist eine in der Praxis bewährte Lösung, die auch bei uns perfekt funktioniert.“ Unterm Strich freut Kemming sich über spürbar schnellere Bearbeitungs- und Werkzeugwechselzeiten.
KeraTür GmbH & Co. KG 46348 Raesfeld www.keratuer.de
​​
BM-Fotos: Christian Närdemann